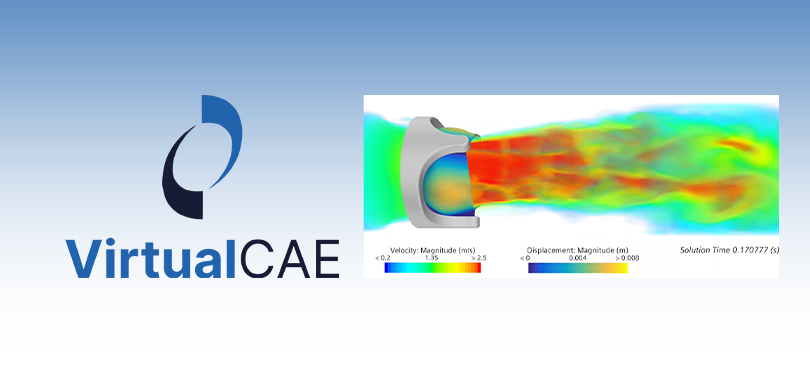
ISO 5840-1 Certification: Challenges in CAE Simulation of Heart Valves
- VirtualCAE
- 16/02/2025
- Blog
- CFD, English, Heart Valves, Simcenter STAR-CCM+
- 0 Comentários
With the growing demand for cardiovascular disease treatments, the use of biomaterials, especially heart valve prostheses, has expanded.
Manufactured from porcine valves or bovine pericardium tissue, these prostheses provide an effective solution for patients requiring valve replacement. To ensure these prostheses meet performance and safety requirements, structural analysis (FEA) combined with computational fluid dynamics (CFD) has become vital in the certification process. This approach allows for an accurate assessment of valve behavior throughout the cardiac cycle, providing valuable insights into its operation and interaction with blood flow.
The ISO 5840-1 standard establishes certification criteria for heart valve prostheses, covering aspects such as fatigue resistance and hidrodynamic performance under simulated conditions to ensure long-term efficacy and safety. Among the key factors analyzed under this standard are thrombogenic potential, hemolysis index, and cyclic structural stresses, as well as their effects on valve durability. The thrombogenic potential assesses the likelihood of blood clot formation, while the hemolysis index measures the occurrence of red blood cell rupture—both representing significant health and safety risks for patients.
These simulation criteria and requirements set by ISO 5840-1, particularly Annexes H and K, are fully met by VirtualCAE. The CAE methodology employed in these simulations ensures that the valve complies with the strict performance and safety criteria necessary for efficient and safe blood pumping in patients. Additionally, this approach verifies whether the valve structure is adequately designed to withstand the stresses generated during opening and closing cycles, ensuring its durability over millions of cycles.
Heart valve prosthesis simulations are highly complex due to the dynamic and nonlinear nature of blood flow, as well as the significant deformation and displacement of leaflets during valve operation throughout the cardiac cycle.
Fluid-Structure Interaction (FSI) is essential to accurately capture shear forces, as well as areas of turbulence and stagnation in blood flow—critical factors for thrombus formation and hemolysis occurrence. The movement of the leaflets directly influences the flow behavior, requiring a model that properly represents the pulsatile nature of blood flow and the coupling between the fluid and solid domains. Furthermore, as the thin leaflets displace a substantial amount of blood and experience large pressure variations, the model must handle significant deformations and high accelerations throughout the cardiac cycle.
The modeling of strongly coupled FSI simulations presents inherent challenges due to the different physics and dynamics governing fluids and solids, each ruled by distinct equations and discretization methods. The fluid follows the Navier-Stokes equations for incompressible flow, while the solid obeys a hyperelastic material law. Additionally, two physical conditions must be met at the fluid-structure interface: the kinematic condition, which requires identical velocities at the fluid-solid surfaces to ensure cohesive movement, and the dynamic condition, which balances pressures and forces on both sides of the interface.
Given this complexity, advanced technical expertise and robust simulation tools are essential to accurately capture the involved phenomena. VirtualCAE, with its expertise in FSI simulations, conducts these specialized analyses, ensuring that heart valve prostheses are certified under real-world operating conditions, while also driving technological development and innovation in the biomedical field.
Get in touch and find out more about the services and products offered by VirtualCAE. ✅